Exploring the Various Methods and Technologies Behind Plastic Extrusion
The realm of plastic extrusion is a mix of accuracy, modern technology, and innovation, crucial to numerous industries worldwide - plastic extrusion. Advanced equipment, computerized controls, and an array of products merge in this intricate procedure, generating high-quality, durable products. As the sector advances, a change in the direction of sustainable materials and intelligent equipment is noticeable. The adhering to conversation will clarify these modern technologies and methods, while likewise hinting at the exciting future prospects of this essential manufacturing process.
Comprehending the Basics of Plastic Extrusion
The procedure of plastic extrusion, typically hailed as a keystone in the world of production, forms the bedrock of this discussion. In essence, plastic extrusion is a high-volume manufacturing process in which raw plastic material is melted and developed into a constant profile. The process begins with feeding plastic products, commonly in the kind of pellets, right into a warmed barrel.
The Function of Different Materials in Plastic Extrusion
While plastic extrusion is a frequently made use of technique in manufacturing, the materials made use of in this process significantly affect its last result. Various kinds of plastics, such as abs, polyethylene, and pvc, each offer unique homes to the end product. Producers need to meticulously consider the residential properties of the material to optimize the extrusion procedure.
Strategies Made Use Of in the Plastic Extrusion Refine
The plastic extrusion procedure entails numerous strategies that are crucial to its operation and efficiency (plastic extrusion). The discussion will certainly start with a streamlined explanation of the essentials of plastic extrusion. This will certainly be adhered to by a malfunction of the process in detail and an exploration of techniques to enhance the efficiency of the extrusion strategy
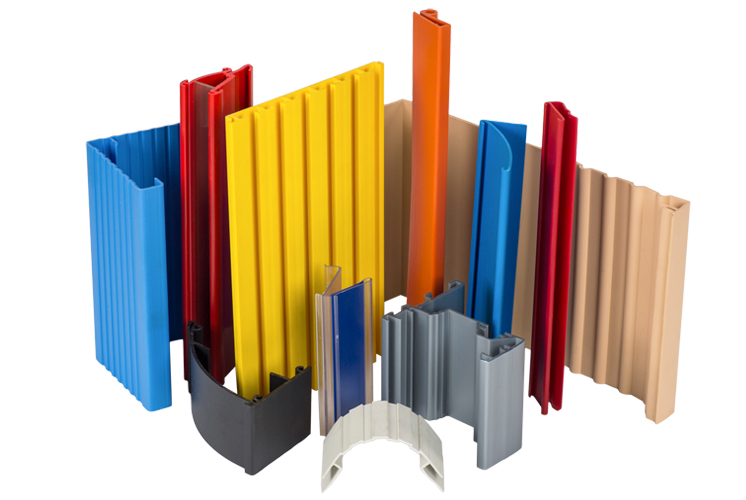
Understanding Plastic Extrusion Fundamentals
In the world of production, plastic extrusion stands as a basic process, essential in the production of a plethora of everyday things. At its core, plastic extrusion involves transforming raw plastic product right into a continual profiled form. This is attained by melting the plastic, commonly in the kind of pellets or granules, and forcing it with a designed die. The resulting item is a lengthy plastic item, such as a cable, pipeline, or panel coating, that maintains the form of the die. This cost-effective method is highly flexible, able to produce intricate forms and fit a wide array of plastic products. Fundamental understanding of these fundamentals enables additional expedition of the more intricate aspects of plastic extrusion.
Detailed Extrusion Process Failure

Improving Extrusion Method Efficiency
Effectiveness gains in the plastic extrusion procedure can considerably impact both the high quality of the end product and the overall efficiency of the procedure. Continual optimization of the extrusion technique is essential to preserving an affordable edge. Strategies that improve performance typically entail accurate control of temperature level and pressure throughout the procedure. Modern modern technologies, such as electronic systems and sensing units, have actually contributed in attaining this control. Additionally, the usage of high-grade resources can reduce waste and enhance outcome top quality. Routine upkeep of extrusion equipment can additionally decrease downtimes, therefore boosting performance. Embracing lean manufacturing principles can assist get rid of unnecessary actions in the procedure, advertising effectiveness gains.
Exactly How Innovation Is Altering the Face of Plastic Extrusion
The introduction of new modern technology has actually substantially transformed the landscape of plastic extrusion. It has led to the growth of sophisticated extrusion machinery, which has actually improved the performance and top quality of the plastic extrusion procedure. In addition, advancements in the extrusion procedure have actually likewise been driven by technological innovations, using improved abilities and plastic extrusion adaptability.
Advanced Extrusion Equipment
Reinventing the world of plastic extrusion, advanced machinery imbued with advanced innovation is ushering in a new age of efficiency and precision. These machines, equipped with innovative features like automatic temperature level control systems, make certain optimum problems for plastic processing, consequently minimizing waste and improving product quality. While these advancements are currently impressive, the constant development of technology assures also greater leaps forward in the area of plastic extrusion equipment.
Developments in Extrusion Processes
Utilizing the power of modern-day innovation, plastic extrusion processes are going through a transformative transformation. With the advent of 3D printing, the plastic extrusion landscape is likewise increasing right into brand-new worlds of possibility. These technological innovations are not just boosting the quality of extruded plastic products however likewise thrusting the industry towards a more sustainable, effective, and ingenious future.
Real-World Applications of Plastic Extrusion
Plastic extrusion, a functional and reliable procedure, locates use in plenty of real-world applications. It's primarily used in the manufacturing industry, where it's used to create a myriad of products such as pipelines, tubings, window frameworks, weather condition stripping, and fencing. The automotive market likewise utilizes this technology to produce components like plastic and trim bed linen. In addition, the clinical area depends on extrusion for the construction of catheters, IV tubing, and various other clinical devices. Even in food manufacturing, extrusion contributes in developing products like pasta or cereal. The toughness and flexibility of plastic extrusion, combined with its cost-effectiveness, make it an important process throughout different sectors, underscoring its widespread practical applications.
The Future of Plastic Extrusion: Trends and forecasts
As we seek to the perspective, it becomes clear that plastic extrusion is positioned for substantial developments and transformation. New technologies assure to transform the market, from smart machinery that makes the most of performance to lasting materials that decrease environmental effect. Automation and robotics are forecasted to play a larger duty, streamlining production and guaranteeing consistent top quality. Environmentally friendly alternatives to traditional plastic, such as bioplastics, are additionally anticipated to obtain grip. These materials not only help to save sources but likewise lessen waste, straightening with international sustainability objectives. Developments in 3D printing are anticipated to open up new possibilities for personalization. These trends indicate a vibrant, developing future for plastic extrusion, driven by technological innovation and a commitment to sustainability.
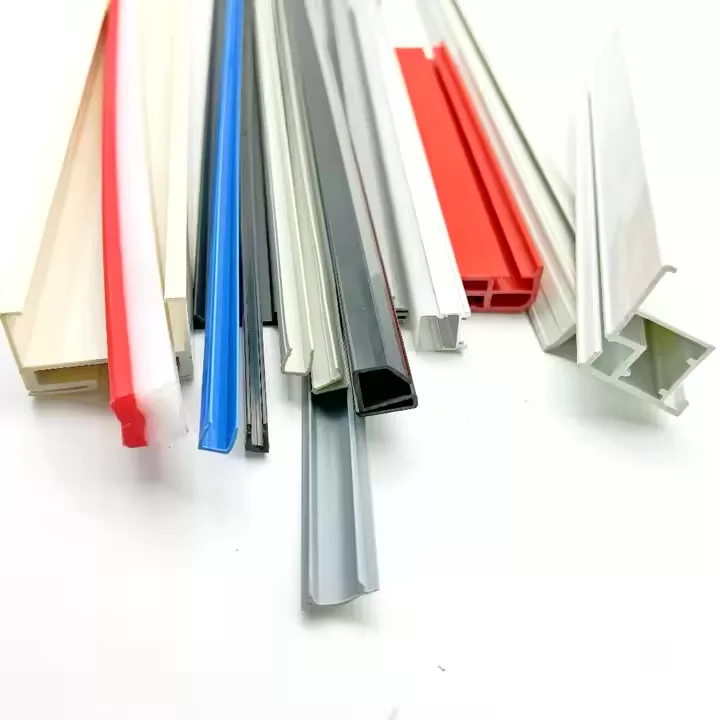
Conclusion
Finally, plastic extrusion is a complex procedure that utilizes sophisticated modern technology and differed materials to produce varied items. Technical improvements, such as computerized controls, improve the production process and make sure regular results. Additionally, the sector's concentrate on sustainability and intelligent machinery suggests an appealing future. As plastic production continues to progress, it stays a vital part of numerous industries worldwide.
In essence, plastic extrusion is a high-volume manufacturing process in which raw plastic product is thawed Our site and developed into a continuous profile.While her explanation plastic extrusion is a generally made use of method in manufacturing, the materials made use of in this procedure considerably affect its last outcome. At its core, plastic extrusion involves transforming raw plastic product right into a continuous profiled form. It has actually led to the development of advanced extrusion equipment, which has enhanced the efficiency and high quality of the plastic extrusion procedure.In final thought, plastic extrusion is a complicated process that uses innovative innovation and varied materials to develop diverse items.